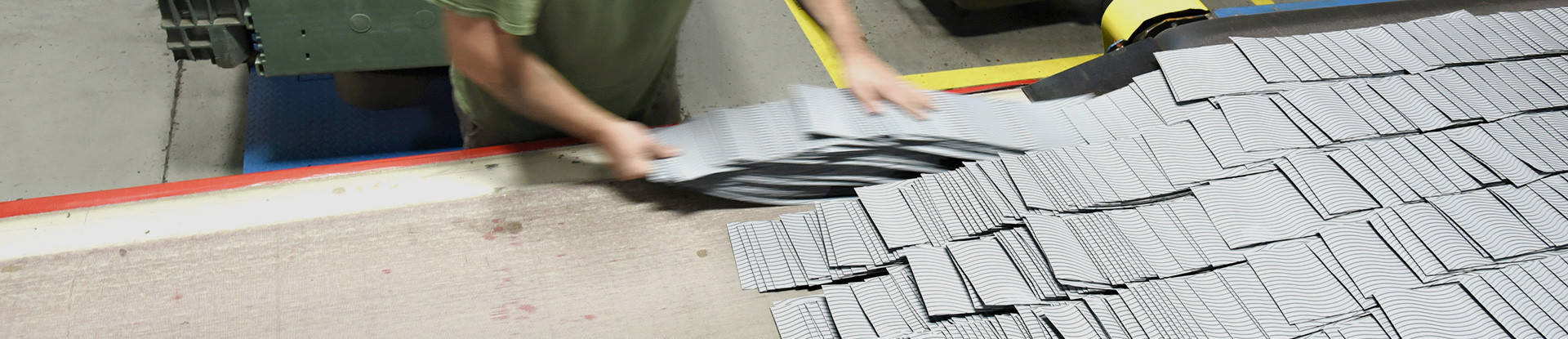
The Capacity to Deliver
We own an exceptional source of supply. With a combined output of battery separators, customers worldwide can rely on Daramic to deliver. It's our consistent three step approach to manufacturing that has ensured the highest quality product day-in, day-out for many decades.
Step 1: Mixing/ ExtrusionIndustry leading raw materials are weighed and measured to the formula requested by our customers, where they are blended together and passed through the extrusion process. Upon exit from the extruder, the material is immediately ‘calendered’, which is an embossing of the sheet with the customers required profile. In preparation for the next step, the material is wound in a roll and cooled. |
![]() |
Step 2: ExtractionThe porous characteristics
of the separator is provided through the process of extraction. This step involves the unwinding of the
extruded roll, a trip through the extracting bath, followed by a pass through a
high temperature. During this step,
special customer specific additives & coatings are added. Once complete the separator roll takes on its
final grey coloring.
|
![]() |
Step 3: FinishingIn preparation for customer shipping & delivery the material is prepared in two primary ways - roll form or cut piece. Ensuring industry-leading quality and reliability Daramic provides: •
Multiple
inspection steps
•
Flexible,
high-speed finishing to enable customized solutions
• State-of-the-art slitters deliver uniform width control |
![]() |
Quality Controlled
To ensure the highest quality in all aspects of our business, Daramic has integrated principles of six sigma & lean manufacturing into its operating system. Daramic's dedicated employees strive to enhance overall product quality, improve processes, reduce waste & minimize variation throughout the entire enterprise.
Daramic's world-class manufacturing has achieved ISO Quality Certificates:
ISO 14001: 2015
ISO 9001: 2015
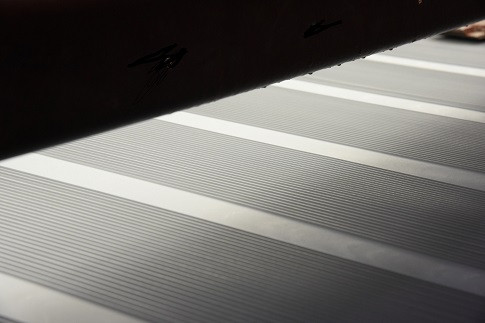
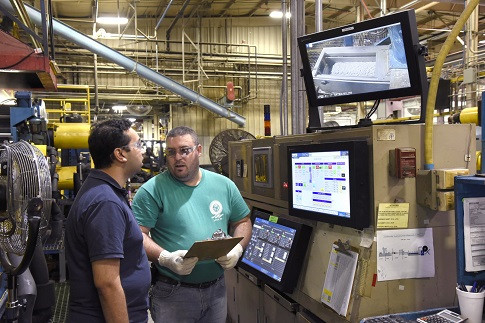
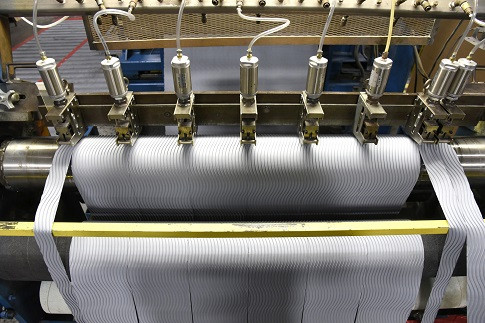